We rely on electrical equipment for so many aspects of our lives, from computers and phones to appliances and tools. But while most of us use electrical equipment on a daily basis, many of us don’t think about the potential hazards that can pose a serious threat if precautions aren’t taken. Testing and tagging companies like Precision Test and Tag check appliances and other electrical devices to identify faults and keep us safe from these dangers.
What is Electrical Testing and Tagging?
Thousands of accidents from electrical faults happen each year. In some cases, these accidents can even be fatal. That’s because electrical items can develop faults over time, and if they’re not properly maintained, these faults can lead to accidents.
To help prevent these accidents, all electrical equipment must be regularly tested and tagged to make sure it is safe to use. Testing involves using a Portable Appliance Tester (PAT) to check that the appliance is working correctly and is not damaged in any way. Tagging involves attaching a label to the appliance that shows when it was last tested and when it needs to be retested.
Testing and tagging help protect both people and equipment in the workplace by minimising the risk of an electrical hazard, such as an electric shock or fire. This process enables you to identify potential risks and take steps to mitigate them. In other words, it helps you avoid electrical-related accidents before they happen.
SafeWork NSW Requirements
Since the introduction of Work Health and Safety (WHS) laws in Australia, SafeWork NSW has been responsible for regulatory compliance and enforcement. This includes ensuring that all workers are safe from potential hazards in the workplace, like those associated with electrical equipment.
Many people don’t know that any appliance with a cord can potentially become an electrical hazard. Common situations where appliances become hazards at work are when they are:
● Left plugged in and unattended;
● Damaged or have frayed cords;
● Being pinched or constricted by furniture or other objects; and
● Connected to an overloaded circuit
One way of managing these potential hazards is through required testing and tagging. This helps to ensure that workers are aware of any risks associated with specific materials, and can take appropriate precautions when working with them. Compliance with SafeWork NSW requirements is therefore essential for the safety of all workers in New South Wales.
If you are an employer or run a business, you are responsible for making sure that all electrical equipment in the workplace is regularly inspected and tested by a licensed professional. This is especially important if the equipment is exposed to conditions that could damage it or shorten its expected lifespan. Some examples of such conditions include exposure to moisture, heat, vibration, mechanical damage, corrosive chemicals, or dust.
By making sure that the electrical equipment undergoes regular testing and tagging, you can help it continue to operate safely and efficiently.
Reducing the Risk of Injuries at the Workplace
High voltage electricity is extremely hazardous and might result in severe injuries. For example, contact with live electrical wires could result in shocks and burns, while faulty electrical equipment could cause fires and explosions. Therefore, it is important to be aware of the dangers of high voltage electricity and take necessary precautions to avoid injuries at the workplace.
The goal of testing and tagging is to reduce the risk of electric shocks or electrocution by making sure that every outlet or piece of equipment has been inspected and tagged for electrical hazards. Once these dangers are identified, they can be mitigated through specific control measures, such as safety labelling, insulation, grounding, and using personal protective equipment (PPE).
Testing and tagging help to ensure that all devices are safe to use and that any potential hazards are identified and addressed. By taking this simple step, businesses can help to create a safer working environment for everyone.
Helps Prevent Fires and Explosions
Electrical fires are more common than you might think, and they can be extremely dangerous. Industrial or manufacturing companies hold flammable liquids that can cause an explosion upon contact with an ignition source like a spark. This risk is even greater in the oil and gas industry due to the high amounts of flammable vapours that are present from mobile engines and auxiliary motors on site.
Another way that electrical fires can start is when faulty wiring sparks behind walls. Additionally, employees misusing appliances or equipment can also lead to fires in office spaces. Even health care facilities are at high risk of electrical fires because of the seemingly endless list of electrical equipment that can overload sockets.
By testing and tagging electrical equipment, safety officers can identify these faults and take the necessary corrective action. Additionally, proper maintenance of electrical equipment will also help to prevent fires, as worn or damaged parts can often lead to overheating or arcing.
Since electricity can be a source of ignition, it’s important to ensure that all electrical equipment is in good working order and is properly maintained. Regular testing and tagging of electrical equipment can achieve this, while also ensuring the safety of employees and occupants.
The Need for Professional Testing and Tagging in the Workplace
Any place that has electrical equipment present is at risk of electricity-related accidents. That’s why it’s so important to make sure that all electrical equipment regularly undergoes proper testing and tagging. Not only are these measures required by law, but they also help reduce the risk of injuries and prevent fires.
Often, testing and tagging appointments are only booked after an incident has occurred where someone has been electrocuted or there has been an electrical fire. Remember that these dangerous situations are preventable.
The AS/NZS 3760 is the Australian Standard that provides guidelines and regulations for the test and tag industry with regard to the electrical safety of appliances in the workplace.
It’s important to note that only a licensed professional should carry out testing and tagging. This is because they have the necessary knowledge and experience to properly identify any potential hazards. Additionally, licensed professionals also have the right tools and equipment to carry out the task safely and correctly to create a safer working environment for everyone
So if you haven’t had a regular inspection done, it’s time to schedule one right away. Taking these simple precautions could end up saving lives.
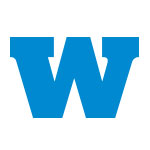
Weekender Newsroom
This post has been published by the team in our newsroom.