Businesses everywhere are going digital, and manufacturers are no exception. Digital tools like payroll management systems and prototyping software are becoming commonplace among Australian manufacturers, and any company that does not embrace digital transformation is likely to fall behind its competitors.
From improving internal communications to boosting production efficiency, digital technologies are transforming Australian manufacturers in many important ways. In this article, we’ll take a look at some of these strategies and how manufacturers can use them to improve efficiency and decrease costs.
Here are just some of the most high-value digital transformation strategies that Aussie manufacturers are implementing in their factories and warehouses today.
Powering Factories Sustainably
Digital transformation initiatives that are concerned with plant energy upgrades can help manufacturers power their factories more sustainably, ensuring facilities are ready and equipped to participate in Australia’s transition to renewables. For Aussie manufacturers, making the switch to sustainable energy involves investing in commercial solar systems, smart switches for power-saving, and environmental IIoT devices for ESG monitoring.
Manufacturers can employ digital energy management systems that allow them to track energy consumption over long periods of time. This data then allows them to build predictive models for energy consumption in the future, making allowances for peak periods.
Sensors can also be attached to energy production equipment to detect inefficiencies. Companies can then repair or replace equipment that isn’t functioning at full capacity in order to boost the efficiency of energy production. By using digital tools and investing in renewable energy systems like solar, manufacturers can take full advantage of renewable energy, lowering costs and decreasing environmental impact.
Improved Human Resource Management
While digitisation is a trend that doesn’t show any signs of stopping, manufacturers will always have a need for human employees. From factory workers on the ground to tech specialists responsible for troubleshooting problems with digital systems, people are essential to a properly functioning factory.
Manufacturers can use a variety of digital tools to more efficiently manage their workforce. For instance, instant messaging platforms like Slack and WhatsApp allow for quick company-wide communications, while video conferencing tools like Zoom and Skype make speaking with remote employees incredibly easy.
HR departments can also use automated payroll tools to simplify the process of computing employee wages and issuing paychecks. They can also leverage digital recruitment tools to onboard employees on a larger scale, allowing for streamlined staff orientation and training procedures.
Digital Product Development
Research and development (R&D) refers to the development of new products and technology. An Australian manufacturer can distinguish itself from its peers by committing to R&D as part of their overall business strategy. Digital transformation is a great way to make this process more efficient and viable. For example, companies can employ big data and machine learning to understand market trends and customer pain points to either optimise an existing product or create a new one.
Companies can also make the R&D process more efficient by using digital product design tools, which allow for faster digital modelling and prototype creation. By embracing digital transformation, Australian manufacturers can make innovation a bigger part of their day-to-day operations.
3D Printing
In 2024, 3D printing should be a significant part of any manufacturer’s digital transformation strategy. Factories can implement 3D printers in different stages of the production process by using them to create components of the finished products.
There are many benefits to 3D printing. For instance, they can produce goods with better accuracy than human factory workers and many robotic tools. This leads to a reduction in waste and lower costs. Factories can also use 3D printers to save on raw materials by using recycled materials as feedstock for the printers.
Australia is investing heavily into recycling manufacturing plants nationwide not only for plastic but also for glass and even metals. With Visy opening a glass recycling facility right here in Penrith earlier this year and producing new jobs alongside boosting the local economy, it’s evident that the unique relationship between the manufacturing sector and Australia’s Sustainable Development Goals will only continue to be explored over the coming decade.
There is much to be said about the resourcefulness of 3D printing and the position of this tech in a circular economy, where production lines are optimised to be just as adaptable as they are streamlined. Embracing 3D printing also allows companies to be a lot more flexible when it comes to making minor changes to products. Designers can use prototyping software to edit product models and feed them into 3D printers, which can then produce items based on the new models without the need to cease production in order to make manual changes to industrial printers and other equipment.
Artificial Intelligence
No discussion of digital transformation strategies is complete without mentioning artificial intelligence – arguably the most impressive technological feat of the decade, and a digital tool with seemingly exponential potential. AI can be used to perform tasks that would take a long time for human employees to complete in a fraction of the time, boosting efficiency and lowering costs. There are now more resources than ever for businesses wanting to use AI, so there’s no excuse not to take advantage of it.
One area of manufacturing on which AI has had a massive impact is predictive maintenance, which involves determining when manufacturing equipment should be repaired or replaced before it breaks down. This is done by installing sensors on the equipment and feeding the data gathered into an AI tool. Predictive maintenance saves manufacturers the cost of having to wait for tools to get damaged before repairing them and creates a safer working environment for the human labourers working with these tools.
AI can also be used in areas like quality control, production automation and inventory management. By incorporating AI into day-to-day operations, factory managers can complete these tasks and others with greater speed and accuracy than is possible with human employees.
~
Digitisation is transforming the manufacturing industry. A host of digital tools, including 3D printers, AI-powered predictive software and digital prototyping tools are allowing manufacturers to perform day-to-day tasks more effectively and at decreased costs. This boost in efficiency allows Australian manufacturers to differentiate themselves from their competitors. By using any of the digital transformation strategies outlined above, Aussie manufacturers can improve efficiency, lower costs, and ensure their facilities operate like a well-oiled machine all throughout the digital age and beyond. And speaking more locally, these digital-ready developments can also aid western Sydney in its economic growth, supporting us in becoming a bona fide powerhouse of industry for the Australian economy.
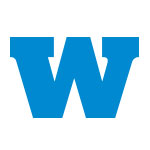
Weekender Newsroom
This post has been published by the team in our newsroom.